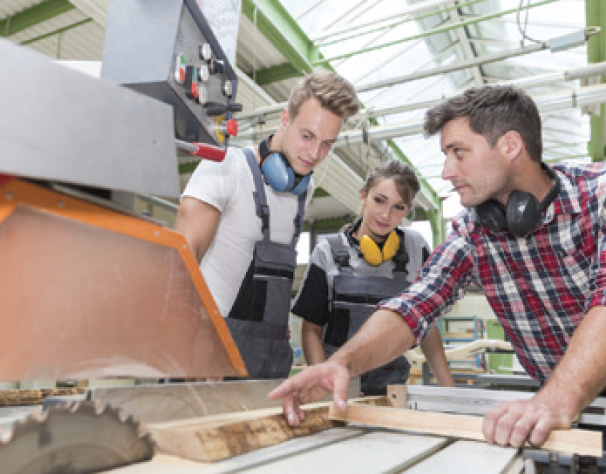
07 Mar
Knowing about hazards is a right
If there are health and safety hazards where you work, you have a right to know about them. Employers are required by law to ensure that you are informed fully about those hazards
While specific right-to-know legislation can differ slightly in various North American jurisdictions, it is basically
the same everywhere.
Employers not only are required to make you aware of hazards, they must ensure that you are trained properly to protect yourself from them.
A major focus of right-to-know legislation in both Canada and the United States is the danger posed by chemicals and other substances.
Canada has the Workplace Hazardous Materials Information System (WHMIS), whose main components are product identification and classification, labeling, safety data sheets and worker training and education. Suppliers, employers and workers all have specified responsibilities.
In the United States, employers are required to inform and train their employees under the Hazard Communication Standard established by the Occupational Health and Safety Administration (OSHA).
In both countries, employers must:
• Provide workers with effective information and training on hazardous chemicals in their work area.
• Keep a current list of hazardous chemicals that are in the workplace.
• Make sure hazardous chemical containers are labeled properly with the identity of the chemical and appropriate hazard warnings.
There are many other hazards that workers need to know about. A common way to classify them is by category:
Biological — bacteria, viruses, insects, plants, birds, animals and humans, etc.
Ergonomic — repetitive movements, improper set up of workstation, etc.
Physical — radiation, magnetic fields, pressure extremes, noise, etc.
Psychosocial — stress, violence, etc.
Safety — slipping/tripping hazards, inappropriate machine guarding, equipment malfunctions or breakdowns.
A Job Safety Analysis (JSA), also known as a Job Hazard Assessment (JHA), is an important way of obtaining and presenting right-to-know information. This is a system to identify and control hazards that can be encountered on
the job.
There are four basic stages
in conducting a JSA:
• Selecting the job to be analyzed.
• Breaking the job down into a sequence of steps.
• Identifying potential hazards.
• Determining preventive measures to overcome these hazards.
A JSA, or a written work procedure based on it, can form the basis for regular contact between supervisors and workers. It can serve as a teaching aid for initial job training and as a briefing guide for infrequent jobs. It can be used as a standard for health and safety inspections or observations. In particular, a JSA will assist in completing comprehensive accident investigations.
Having the right to know is one thing. Making sure you are getting the full benefit of it is another.
That means:
• Taking whatever training is provided.
• Applying the safety rules and procedures you have learned.
• Asking questions whenever you are uncertain about how to be safe in a potentially hazardous situation.
• Being alert for ‘hidden’ hazards and report them immediately.
You are responsible for following all the proper procedures in your job. This includes checking to make sure personal protective equipment (PPE) works properly, knowing how to use it, and making sure you use it.